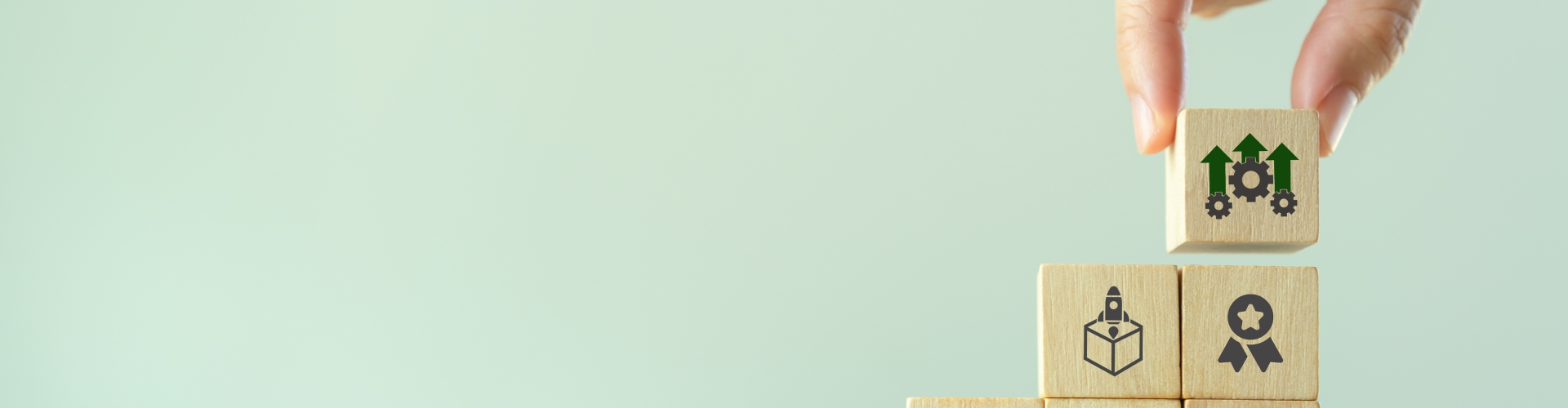
How to reduce total cost of ownership? How to correctly estimate workforce needs? How to avoid equipment downtime and ramp up production?
Thanks to our experience, you will be able to assess your current processes, build a transparent reporting and planning system, develop an effective supplier management model and take your business to a whole new level.
large-scale MRO transformation projects delivered in the last five years
professionals with hands-on experience in EAM transformation and performance improvements for major companies in the CIS
years of combined expertise
OUR SERVICES
MRO operational model
Business processes
- Assessing the maturity of current MRO processes
- Developing improvement initiatives and internal regulations based on target processes
- Developing automation requirements for target processes
- Selecting the best operational model for the MRO function
Organizational structures
- Assessing the current organizational structure and designing a target MRO structure
- Allocating duties among divisions and management levels
- Estimating the required number of repair and maintenance staff
Digital MRO
KPI reporting and dashboards
- Assessing current MRO reporting and KPI functions
- Developing a target set of KPI reports and scorecards
- Designing reporting systems and prototype BI dashboards
Automation
- Implementing/improving repair management IT systems (SAP, 1С, ORACLE, etc.)
- Structuring reference manuals, guides and other reference material
- Digitalizing work/inventory planning systems (MRO automated control systems, mobile workflow apps, etc.)
Supplier relationship management
SLA
- Developing service provider selection procedures for outsourced repairs
- Developing repair schedules for outsourced operations
- Drafting SLA templates
Category strategies
- Developing a methodology and estimating the required levels of emergency stock and minimum supply of spare parts and consumables
- Spare part requirement analysis to inform procurement decisions
- Structuring re-engineering and in-house spare part manufacture processes
Ramping up production
Equipment availability
- Collecting equipment downtime data
- Developing and implementing technical and organizational measures to reduce equipment downtime
- Optimizing equipment maintenance strategies
Equipment performance
- Assessing current equipment performance and production chains
- Developing and implementing measures to improve equipment performance
- Developing and implementing performance monitoring requirements and systems